The long journey from fruit to high-quality product
Processing the fresh fruit immediately upon arrival is the only way to obtain perfect results. That is why during our main season we extract juice and juice concentrate from around 2,000 tons and purees from around 1,200 tons of fruit daily! Cutting edge technology, continuous innovation and 200 employees working 24/7 make it all possible.
It is the only way to guarantee our exacting quality standards.
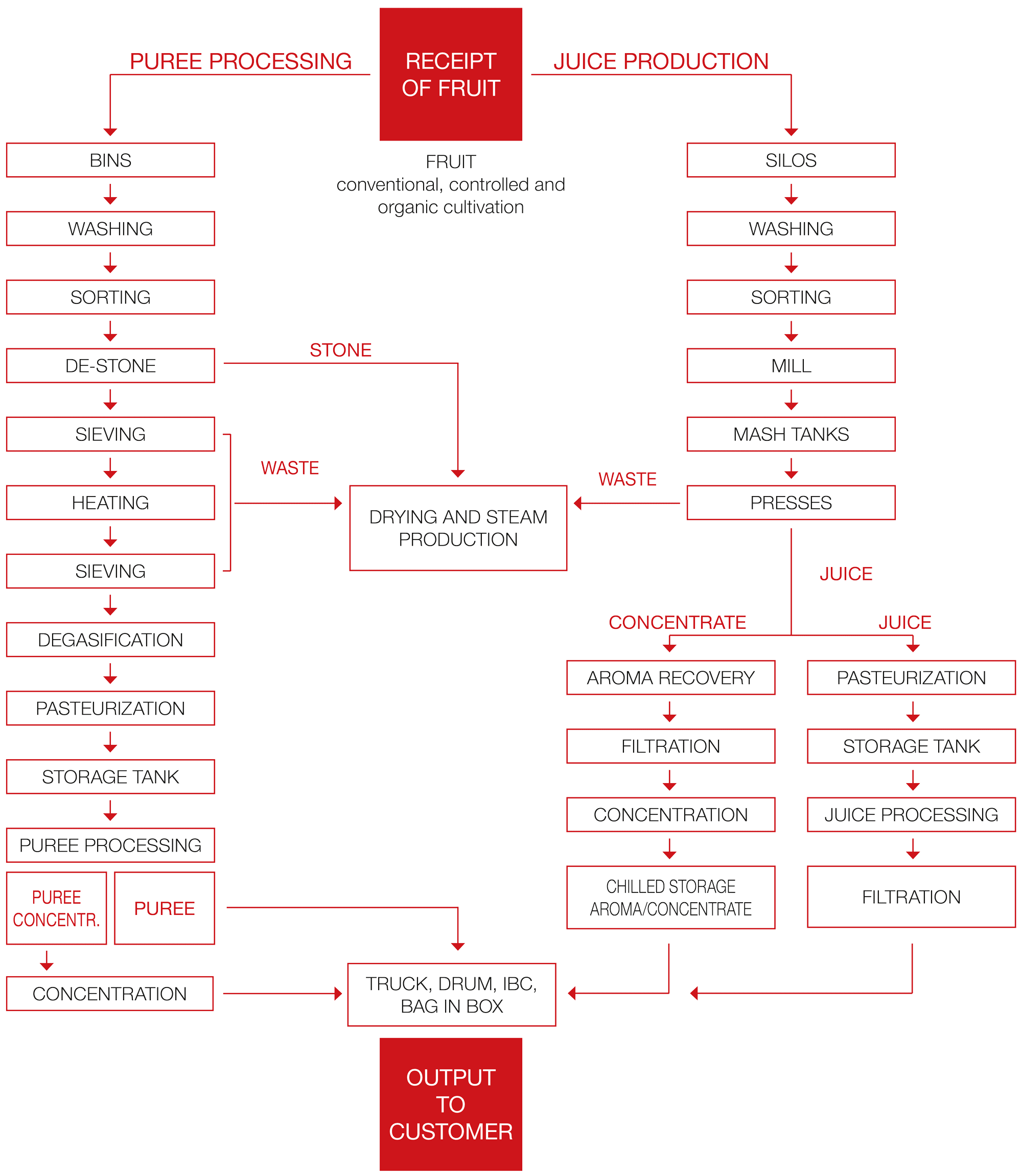
The Harvest
Our purchasing and agronomy team works hand-in-hand with our farmers and suppliers. Only a close and steady exchange of information can guarantee fast delivery of fruit and thus optimal results during the harvest and processing season.
When ripe, the fruit is carefully harvested by the farmers. A crate full of apples can weigh up to 350kg.
The farmers then deliver the crates to collection hubs and co-operatives. From there the fruit is delivered directly to Zipperle. Every hour, countless different types of fruit are being delivered and brought to their respective processing stations.
Depending on the type of fruit, its variety and the desired product, the processing procedures differ, turning the fruit into high-quality semi-finished goods for the global food and beverage industry.
Technology and manpower
At the unloading station, the fruit rolls directly into water baths and is gently carried onwards. Stone fruit are also gently washed and transported across internal water channels. A sophisticated water management system ensures that not a single drop is lost. That is how we not only work more efficiently, by keeping the use of our precious natural resources to a minimum, but also reduce the impact on the environment.
The fruit then floats to the individual stations on fruit washing lines. This protects and already partially cleans the fruit in the process. Small leaves and stems are sieved out.
The fruit is then washed several times and sorted by hand on sorting belts. Only then does the fruit reach the presses and processing lines.
State-of-the-art technology is used throughout the process. During ultrafiltration for example, all particles are filtered out of the juices. What remains is a gently processed, pure and exceptional product without any further additives.
Technology and manpower
At the unloading station, the fruit rolls directly into water baths and is gently carried onwards. Stone fruit are also gently washed and transported across internal water channels. A sophisticated water management system ensures that not a single drop is lost. That is how we not only work more efficiently, by keeping the use of our precious natural resources to a minimum, but also reduce the impact on the environment.
The fruit then floats to the individual stations on fruit washing lines. This protects and already partially cleans the fruit in the process. Small leaves and stems are sieved out.
The fruit is then washed several times and sorted by hand on sorting belts. Only then does the fruit reach the presses and processing lines.
State-of-the-art technology is used throughout the process. During ultrafiltration for example, all particles are filtered out of the juices. What remains is a gently processed, pure and exceptional product without any further additives.
Storage and logistics
Capacity that counts
More than 65 million Litres of juices, concentrates and fruit purees are stored safely in our facilities. Numerous aseptical tanks store juices and fruit purees, partly under controlled temperatures. Concentrates as well as flavours are stored at a constant temperature in cooling tanks.
For their loading and shipment, the aseptical stored products are cooled to 0 °C and prepared in insulated blending tanks. Under our quality assurance’s strict control, sensitive products await their just-in-time delivery in sterile drums, tank lorries or containers.
In addition to the required presentation of a valid cleaning certificate, all lorries are once more strictly checked by quality assurance and disinfected before loading. Reconditioned disposable iron drums are all lined with a second inner bag for greater safety. Returned reusable 1,000 Litre boxes are also thoroughly cleaned before the insertion and filling of new bags.
The very extensive and flexible product preparation and blending allows us to process our customers’ requests as quickly as possible. It will take us a maximum of 72 hours from your order to loading!